Quality
Warehouse
Material reception
Automated control over incoming material through an Auto-Incoming device. This device can read the information from the materials manufacturer labels and identify all relevant information:
- Part number and manufacturer
- MSL
- Data code
- Batch
With this information, our system links the material with our item code with unique ID and the image of the packing unit is stored.
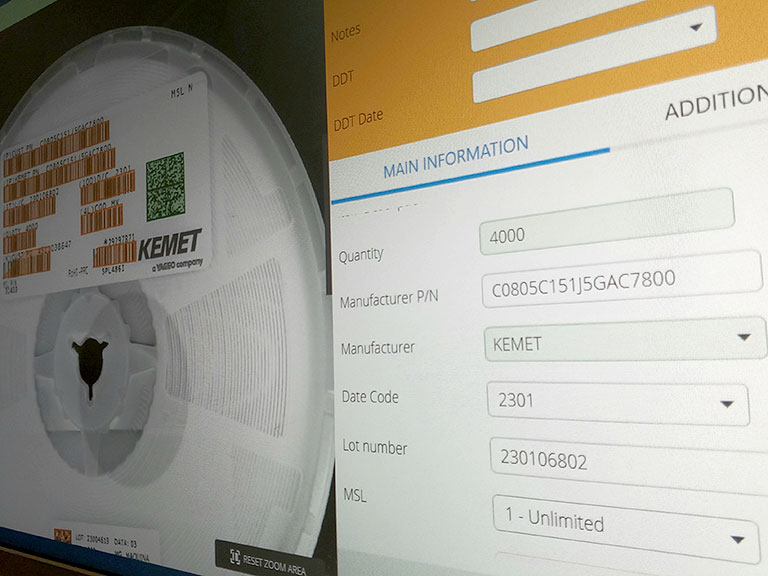
Material storage and preparation
We have smart cabinets to store material. These cabinets control stock through FIFO and smart locations, which makes it easy to prepare orders and assign unique IDs to manufacturing batches.
MSL control, applying the right preventive treatment according to the manufacturer to all items requiring it.
XRAY machine to verify quantities in all reels stored. With this control, we guarantee the veracity of our stock.
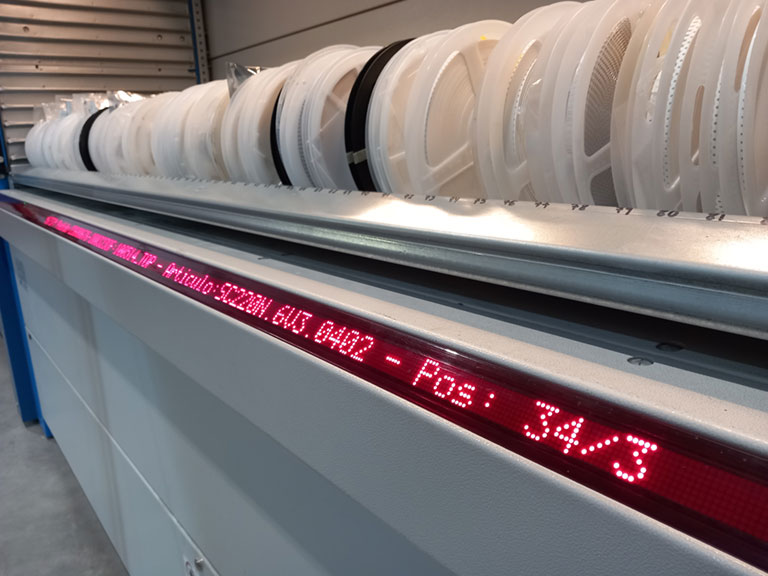
Traceability
All materials assigned to a manufacturing batch are registered through the unique ID. With our traceability system, we can identify which batch is assigned to each component inserted in a circuit, and through the batch we can extract the manufacturer, part number, manufacturing date, and all other information referring to the manufacturer code.
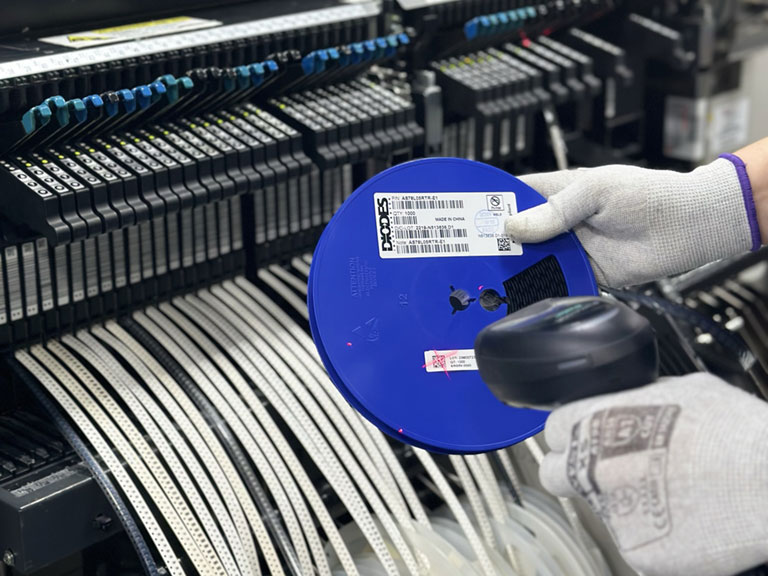
SMD
Assignment of codes and pick&place
Our pick&place machines have a QR code reading system that guarantees validation of the product placed in each feeder.
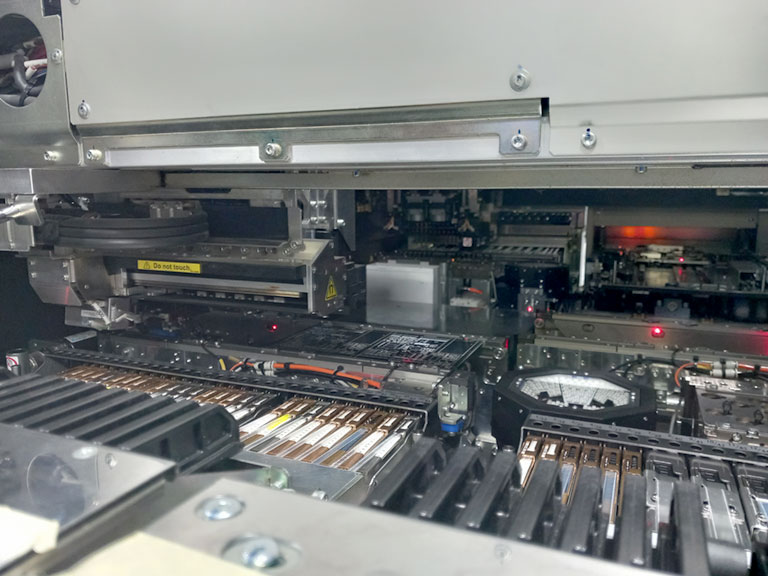
SPI print process control
The printing machines (solder paste printing) has an SPI system (Solder Paste Inspection) that automatically checks to ensure that solder paste is on all circuit pads.

Reflow process control
In the prototyping phase, the profile for our 8-zone furnaces is defined to match the datasheet numbers, always based on IPC standard JEDEC J-STD-020. With specific technology for this purpose, our techniques periodically verify that the furnace’s values are as expected.
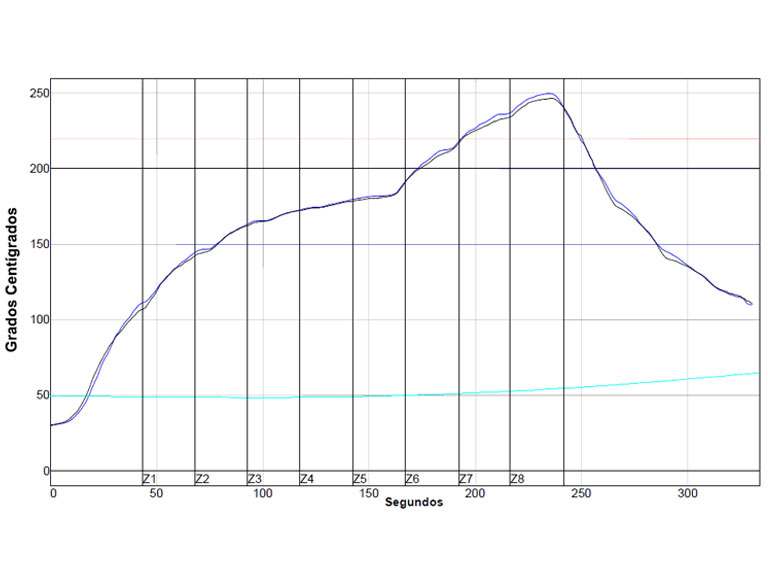
AOI revision
We have AOI inspection devices (Automatic Optical Inspection) with 3D technology. 100% of our production is validated by these devices, which validate all the important aspects of assembly:
- Everything in terms of soldering. Aspects such as the presence and quantity of tin, the soldering bead, etc.
- Presence of overlap
- Polarity
- Coplanarity
- Marking code
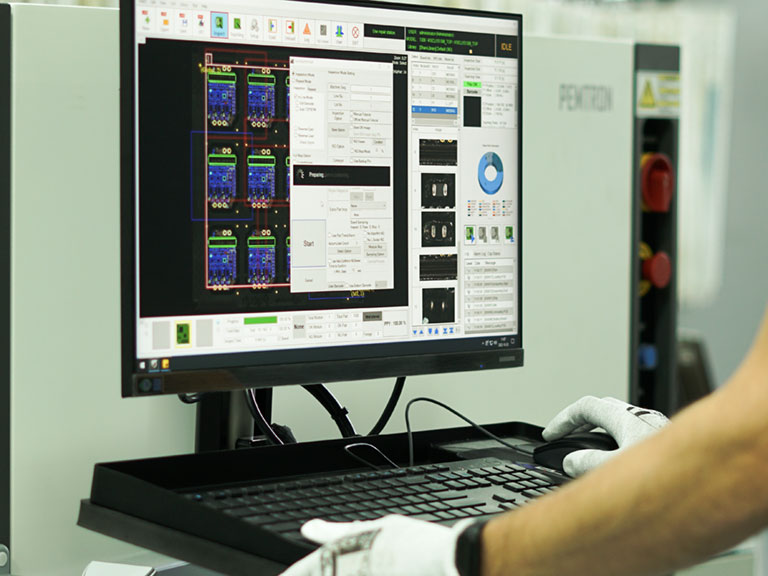
XRAY
All components that AOI cannot revise are inspected with XRAY technology. These components are for when soldering is not visible. BGA, QFN, LGA, LEDS… Both for industrialising a new model and for in-process inspection, it is essential that you have this technology to guarantee assembly quality.
For lighting, both in the industrialisation and in the production phase, XRAY technology provides exhaustive control over voids that are created in the reflow process. These voids directly affect the life cycle of LEDs, and for Montronic it is a priority to reduce the % of voids in soldering to the maximum extent possible.
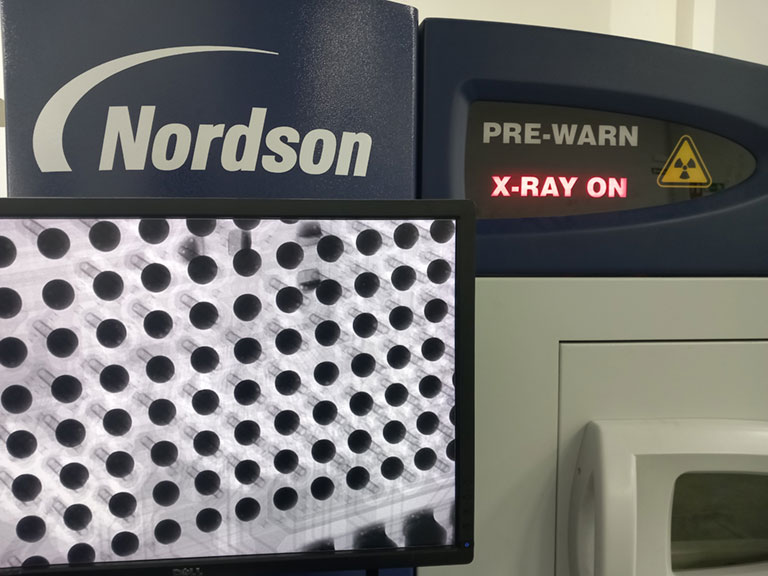
Testing
In the final process phase, we have the human team and technological resources necessary to provide a testing service. Both for the design and manufacture of necessary hardware and for programming and developing the necessary software to conduct however many tests are necessary. We conduct these verifications on tools with tests and more functional end-product verifications to guarantee the quality of the manufactured product.
